Ada 24 Rakyat Malaysia Yang Telah Tempah Ferrari 296 GTB RM1.2 Juta Ini
Harga jualan sepenuhnya Ferrari 296 GTB ini akan melepasi RM3 juta selepas semua kos penghantaran, duti & eksais, cukai dan aksesori dijumlahkan sekali.
Naza Italia, Pengimport dan pengedar rasmi kereta Ferrari (tidak lama lagi SUV juga) di Malaysia, baru sahaja memperkenalkan Ferrari 296 GTB untuk kita media meliur kerana kita tidak dapat mengambil jentera warisan perlumba ini untuk pandu uji on-the-road.
Kenapa? Sebab, dengan 20 unit kereta ini yang ditempah awal oleh bahagian produk dan pemasaran Naza Italia dan dengan bilangan yang tidak begitu mengejutkan, sebanyak 24 unit tempahan diterima hanya sehari selepas pelancarannya, tidak ada keperluan untuk mana-mana media permotoran Malaysia berkongsi pengalaman pemanduan peribadi mereka dengan 296 GTB ini.
Kereta super ini adalah evolusi terkini Berlinetta dua tempat duduk enjin-tengah-belakang Maranello dan kereta yang mentakrifkan semula keseronokan maksimum di belakang roda. Penghantaran Ferrari 296 GTB akan bermula dalam beberapa bulan, tetapi jika anda memesan hari ini, anda mungkin bertuah untuk mendapatkannya dalam masa 24 bulan kerana permintaan global semakin meningkat dan pelanggan Ferrari sedang dipilih untuk membeli kereta eksklusif ini. Ya, anda kena di jemput untuk membelinya.
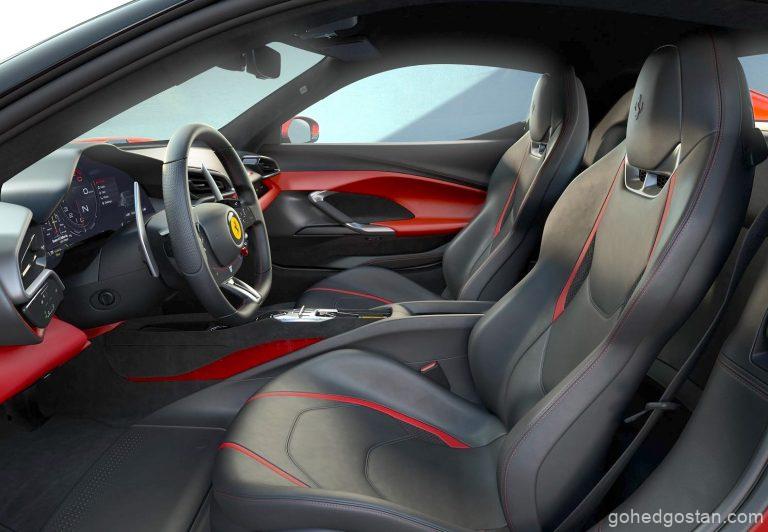
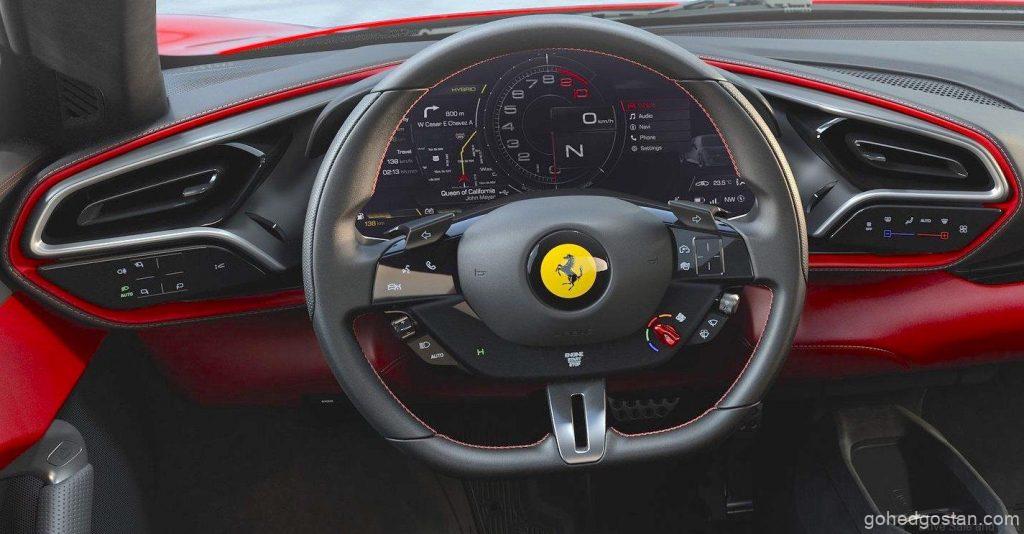
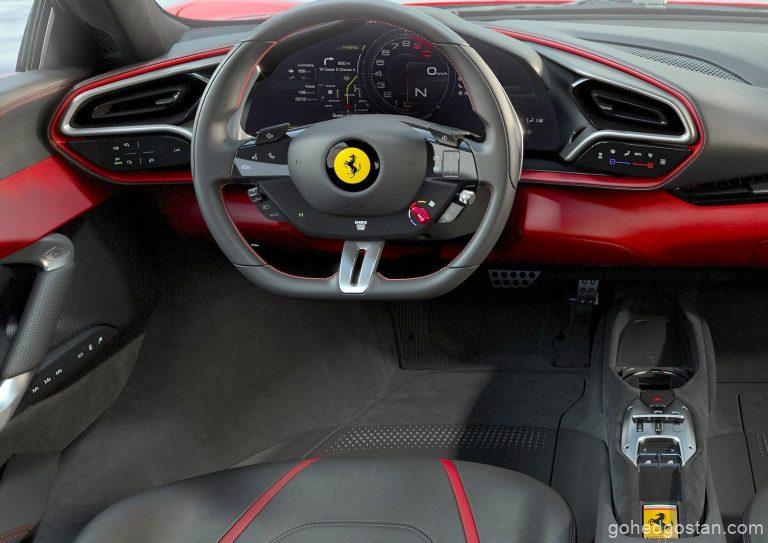
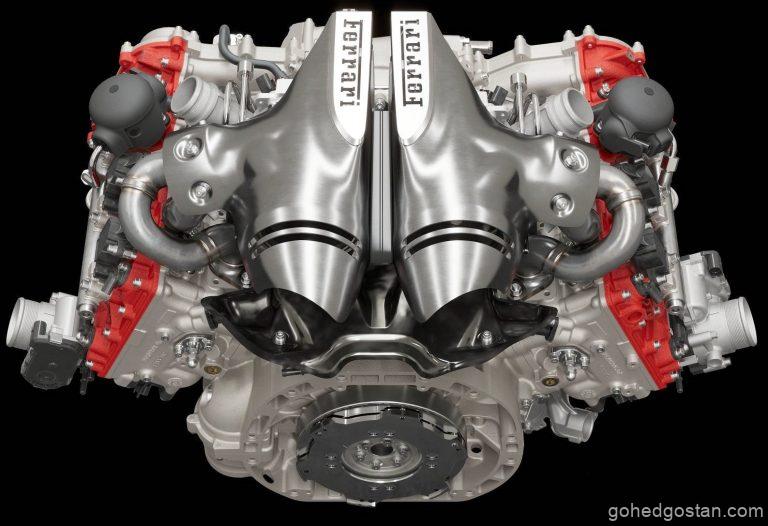
Jadi kami bermimpi sajalah.
Berikut adalah kenyataan media Ferrari dengan lebih maklumat:
First unveiled in June 2021 to the global audience, This Ferrari 296 GTB carries a brand new petrol engine and hybrid powertrain that works together to deliver nothing less that the best driving experience that Ferrari has to offer.
Ferrari’s unparalleled quality standards and increasing focus on client service underpin the extended seven-year maintenance programme offered with the Ferrari 296 GTB. Available across the entire range, the latter covers all regular maintenance for the first seven years of the car’s life. This scheduled maintenance programme for Ferraris is an exclusive service that allows clients the certainty that their car is being kept at peak performance and safety over the years. This very special service is also available to owners of pre-owned Ferraris.
Regular maintenance (at intervals of either 20,000 km or once a year with no mileage restrictions), original spares and meticulous checks by staff trained directly at the Ferrari Training Centre in Maranello using the most modern diagnostic tools are just some of the advantages of the Genuine Maintenance Programme. The service is available on all markets worldwide and from all Dealerships in the Official Dealership Network.
The Genuine Maintenance programme further extends the wide range of after-sales services offered by Ferrari to meet the needs of clients wishing to preserve the performance and excellence that are the signatures of all cars built in Maranello.
This Ferrari 296 GTB is available from the base price of RM1,228,000 (before duties, customization options, taxes and insurance). For further details, contact the Ferrari Malaysia Showroom.
More exciting information about Ferrari Malaysia may be obtained from the official Facebook page: http://www.facebook.com/ferrari.nazaitalia. Follow @ferrari.nazaitalia on Instagram for the latest updates and offerings of Ferrari and Naza Italia.
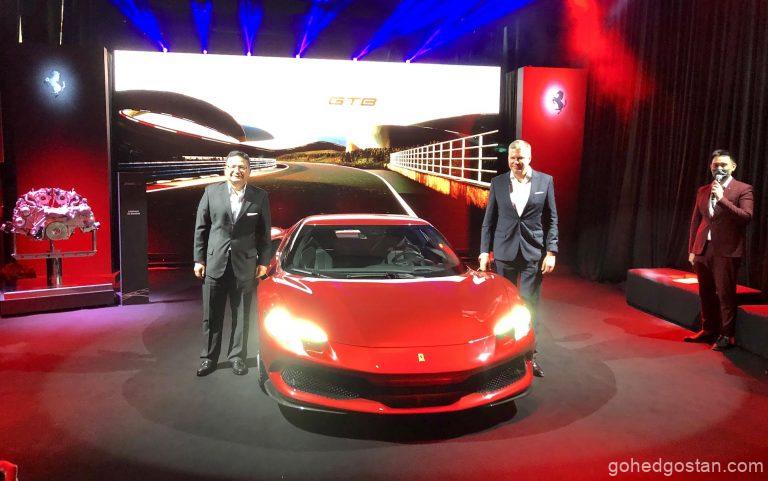
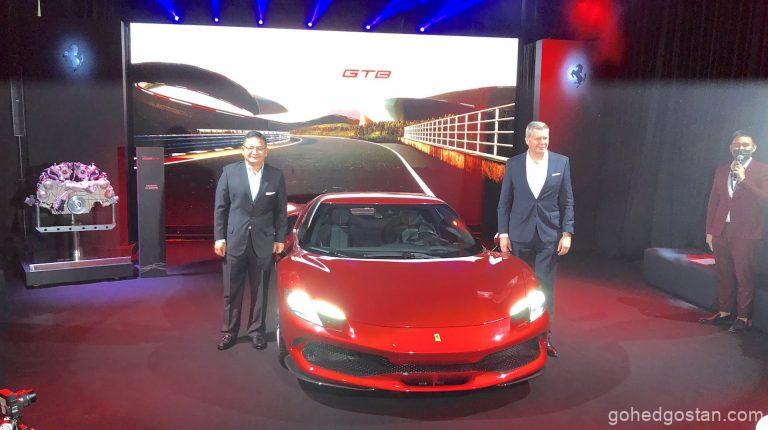
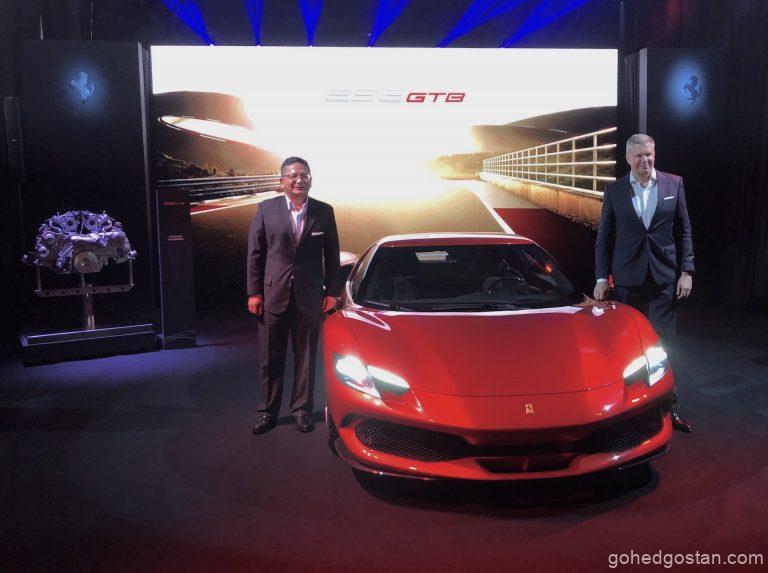
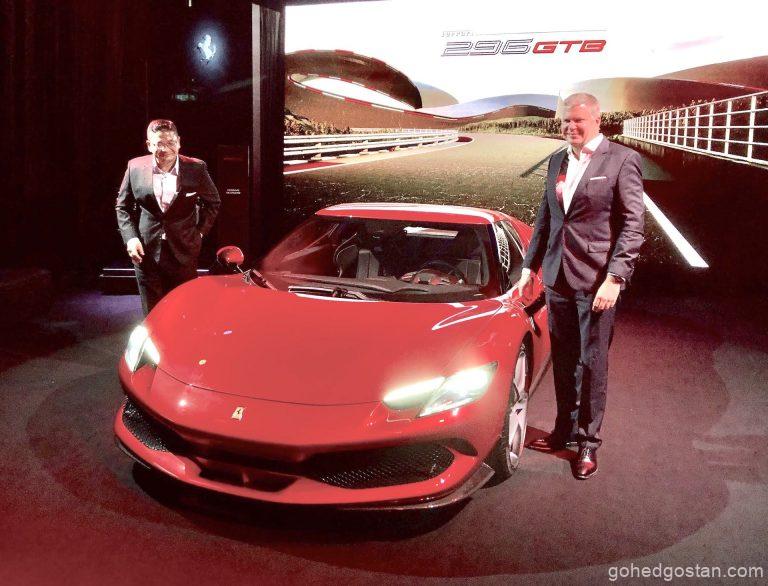
POWERTRAIN
This Ferrari 296 GTB is the first Ferrari road car to sport a V6 turbo with a vee with an angle of 120° between the cylinder banks, coupled with a plug-in electric motor. This new V6 has been designed and engineered from a clean sheet by Ferrari’s engineers specifically for this installation and is the first Ferrari to feature the turbos installed inside the vee.
Aside from bringing significant advantages in terms of packaging, lowering the center of gravity and reducing engine mass, this particular architecture helps deliver extremely high levels of power. The result is that the new Ferrari V6 has set a new specific power output record for a production car of 221 cv/l.
As the V6 turbo is integrated with an electric motor at the rear, the Ferrari 296 GTB’s combined maximum power output is 830 cv, putting it at the top of the rear-wheel-drive sports car segment as well as making it extremely flexible. This is true both in terms of day-to-day contexts (the 296 GTB has a full-electric mode range of 25 km), and in driving enjoyment (accelerator pedal response is instant and smooth at all engine speeds).
The powertrain assembly comprises a V6 turbo ICE, with the 8-speed DCT and E-Diff, and the MGU-K located between the engine and the gearbox. A clutch is set between the ICE and the electric motor to decouple them in electric-only eDrive mode. Lastly there is a high-voltage battery and the inverter which controls the electric motors.
INTERNAL COMBUSTION ENGINE
Thanks to its 663 cv and 221 cv/l, this Ferrari 296 GTB’s ICE sets the new specific power output record for a production road car. Central to achieving this result was the introduction of the 120° vee configuration with equally-spaced firings as well as the positioning of the turbos inside the vee which produces a much more compact engine and optimally distributed masses.
The architecture is also ideal in terms of combustion sequence and the integration of the intake plenums and the engine supports on the intake sides of the cylinder heads. The engine is thus lighter and more compact because of the elimination of the plenums and exterior supports, while the fluid-dynamics benefit from the reduction in volumes, boosting intake efficiency.
The 120° vee architecture, which offers more space between the cylinder banks than a 90° vee, meant the turbos could be installed centrally, thus significantly reducing the unit’s overall size and the distance the air has to cover to arrive in the combustion chamber, maximizing the fluid dynamics and efficiency of the intake and exhaust line ducts.
To obtain this specific power output, the pressure in the combustion chamber had to be pushed to new heights. Boosting the pressure in the chamber demanded exceptional development from both a thermal-fluid-dynamic and structural point of view without compromising on engine weight and reliability.
To that end, Ferrari poured all of its significant expertise in alloys, dimensioning and components into engineering the aluminum engine block and cylinder heads. Both components are new and specific to the new V6 architecture.
The distribution is completely new: drive is transmitted to the pump assembly (water and oil) via a timing chain and to the valve-train via an offset sprocket and a dedicated timing chain per cylinder bank.
The main chain has a dedicated hydraulic tensioner, two bush chains with relative hydraulic tensioner and different calibrations for right and left bank, as well as a dedicated chain for the oil pump assembly. The valve-train, which has roller fingers with hydraulic tappets, has specific intake and exhaust valve profiles.
The engine benefited from the latest Ferrari combustion chamber development introduced on the SF90 Stradale: central injector and spark plug with 350-bar pressure injection system that improves the fuel-air mix in the chamber, performance and reduces emissions.
The intake and exhaust ducts were redesigned and tuned to maximize volumetric efficiency and thus guarantee high levels of turbulence in the chamber.
The IHI turbochargers have been completely redesigned using higher performance alloys. This meant the maximum revs of the turbos could be increased to 180,000 rpm, with a consequent improvement in performance and boost efficiency, which increases by 24 percent.
The symmetrical, couter-rotating turbos are of the mono-scroll type: the technical solutions adopted have reduced the compressor wheel diameter by 5 percent and the turbo rotor 11 percent compared to the V8 applications, despite the very high specific power.
The reduction in the rotating masses (the inertia of the two rotating elements has been reduced by 11 percent compared to the 3.9l V8 solution) has reduced the spool up time ensuring instantaneous power delivery.
The crankshaft is made from nitrided steel. To ensure it has a 120° crank angle, after the initial forging of the rough ingot, the crankshaft is twisted and then subject to a deep nitriding heat treatments (to guarantee resistance to high loads), machining and balancing.
The firing order of the new V6 (1-6-3-4-2-5) is the result of the crankshaft’s journal geometry. 100% of the rotating masses and 25 percent of the alternating masses are balanced, and therefore its level of balance allows loads on the bushings to be reduced without increasing the weight of the engine.
A new variable displacement oil pump was developed to guarantee that the oil pressure is continuously controlled right across the engine’s entire operating range. A solenoid valve, controlled by the engine ECU in a closed loop, is used to control the pump’s displacement in terms of flow and pressure, delivering only the amount of oil required to guarantee the functioning and reliability of the engine, whilst simultaneously providing a reduction in the power absorbed by the pump itself.
On the oil scavenge side, to minimize splashing losses, the suction system was made more powerful using six scavenge rotors: three specific dedicated rotors for the crankcase below the crank throws, one for the distribution compartment and two for the cylinder head compartments.
In Ferrari engines, the intake plenum is normally located in the centre of the vee. However, the V6 hails a paradigm shift in that regard: its plenums are on the side of the cylinder heads and are integrated with the support for the throttle valve. The light thermoplastic material used to make them keeps engine weight down. This solution boosts performance because of the shorter ducts and consequent fluid-dynamic detuning, in addition to reducing time-to-boost as a result of the high pressure line’s smaller volume.
The new architecture also led to the development of a more linear exhaust line located in the upper part of the engine compartment. The shape of the exhaust reduces back pressure and contributes to boosting performance. The exhaust manifold and catalyzer housings are made entirely from Inconel, a steel-nickel alloy that reduces the weight of the exhaust and makes it more resistant to high temperatures.
Sound-wise, the 296 GTB rewrites the rulebook by harmoniously combining two characteristics that are normally diametrically opposed: the force of the turbos and the harmony of the high-frequency notes of a naturally-aspirated V12.
Even at low revs, inside the cabin, the soundtrack features the pure V12 orders of harmonics which then, at higher revs, guarantee that typical high-frequency treble. This Ferrari’s soundtrack matches its performance, creating a sense of unprecedented involvement, and marking the turning of a new page in Maranello’s berlinetta history.
Even to those outside the car, the shrill sound of the engine is instantly recognisable. The first in the F163 engine family, this V6 earned itself the nickname “piccolo V12” (little V12) during the development phase. The 120° V architecture guarantees a symmetrical firing order while the equal-length, tuned exhaust manifolds combined with the single exhaust line outside the hot-V amplify the pressure waves.
These characteristics are what lend such purity to the orders of harmonics, which are further helped by a limiter that hits an impressive 8500 rpm.
The patented “hot tube” has been completely redesigned for the Ferrari 296 GTB and is positioned prior to the exhaust gas treatment systems so that it channels the pure sound into the cabin, further enhancing driver involvement and excitement.
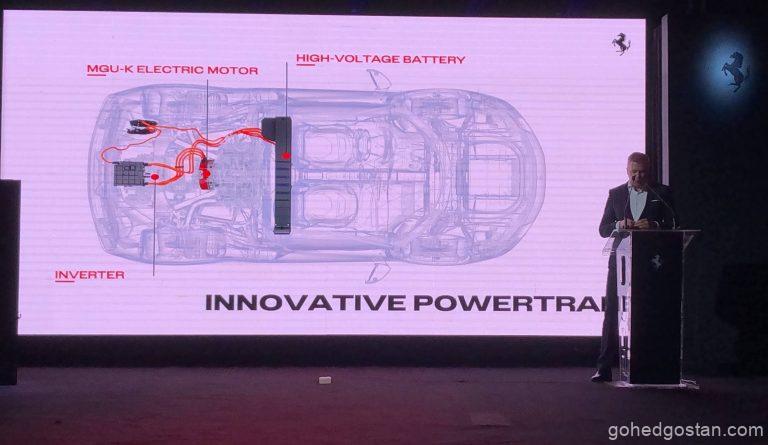
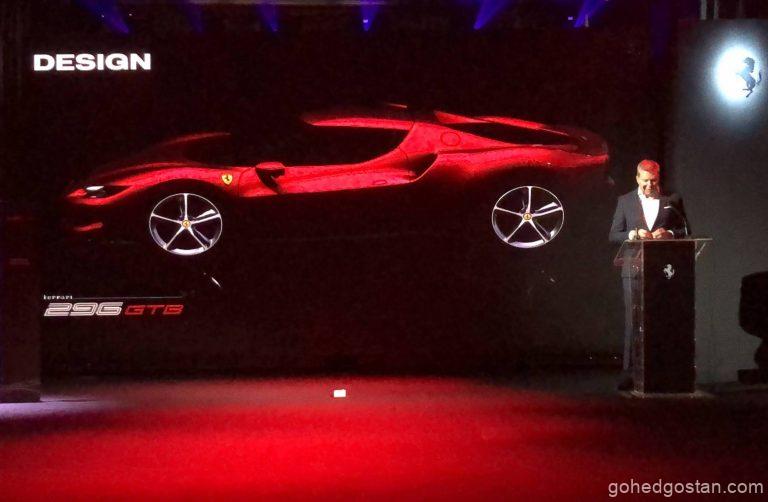
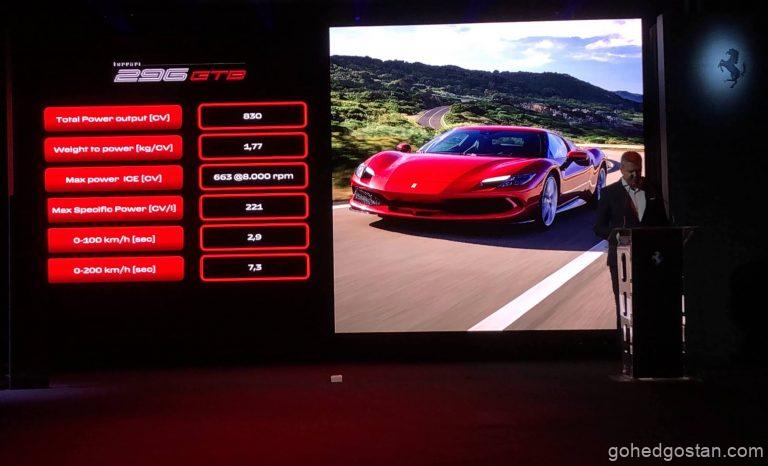
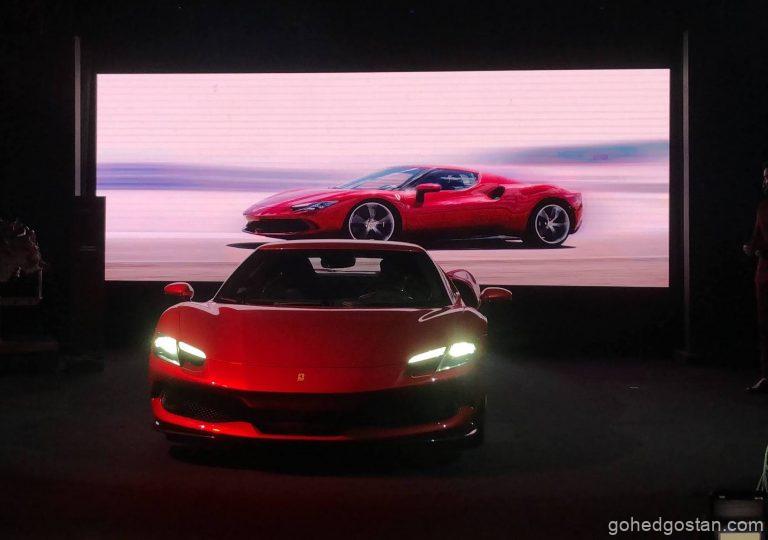
ELECTRIC MOTOR
This is the first ever Ferrari with a rear-wheel drive-only PHEV (Plug-in Hybrid Electric Vehicle) architecture in which the ICE is integrated with a rear-mounted electric motor producing up to 122 kW (167 cv) derived from the Formula 1 application from which it also inherits the MGU-K (Motor Generator Unit, Kinetic) moniker.
The electric motor and ICE communicate via the Transition Manager Actuator (TMA) which allows them to be used both together to produce a combined power output of 830 cv or decouples them to allow the electric motor to run solo.
Aside from the V6 turbo and the 8-speed DCT already adopted on the SF90 Stradale, Ferrari Roma, Portofino M and the SF90 Spider, the powertrain architecture also includes the MGU-K electric motor positioned between the engine and gearbox, the TMA to decouple the electric motor from the ICE, the 7.45 Kwh high voltage battery, and the inverter which controls the electric motors.
The MGU-K is a dual-rotor single-stator axial flux motor. Its compact size and its structure allowed the length of the powertrain to be reduced which, in the final analysis, helped shorten the 296 GTB’s wheelbase. The electric motor charges the high voltage battery, turns on the ICE, supplies it with additional torque and power (up to 167 cv) and allows the car to be driven in all-electric eDrive mode. The MGU-K’s improved design allows it to reach maximum torque of 315 Nm, around 20% more than previous applications.
The TMA (Transition Manager Actuator) allows very rapid static and dynamic transitions from electric to hybrid/ICE mode and vice-versa, thereby guaranteeing smooth, progressive torque. Its control software, which was developed entirely in-house by Ferrari, communicates with the DCT, motor and inverter software to more efficiently manage ICE ignition and its connection and disconnection to the transmission.
Thanks to new generation components, the TMA allowed the design of an incredibly compact transmission: the system has an overall impact on the length of the powertrain of just 54.3 mm. Its architecture comprises a triple-plate dry clutch, a clutch command module in line with the driveline with a clutch control linkage, and ECUs.
Thanks to an innovative design manufactured using laser welding, the 296 GTB’s high voltage battery has a 7.45 kWh capacity and a competitive weight/power ratio. The battery pack is located under the floor and to minimise volume and weight, the cooling system, structure and fixing points are integrated into a single component.
The cell modules contain 80 cells connected in series. Each Cell Supervisor Controller is installed directly in the modules to reduce volume and weight.
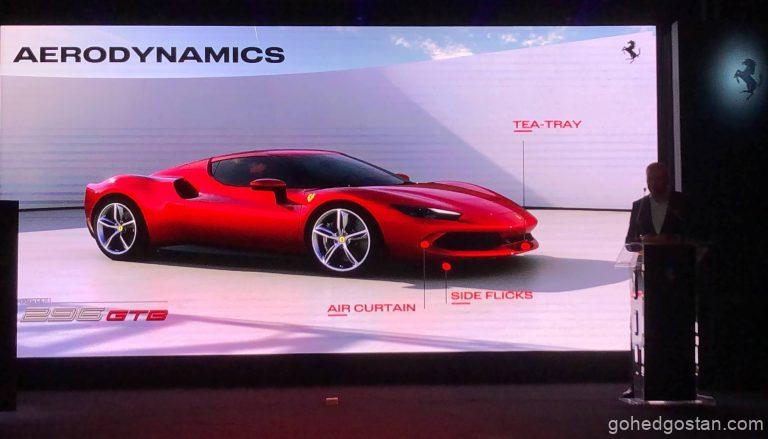
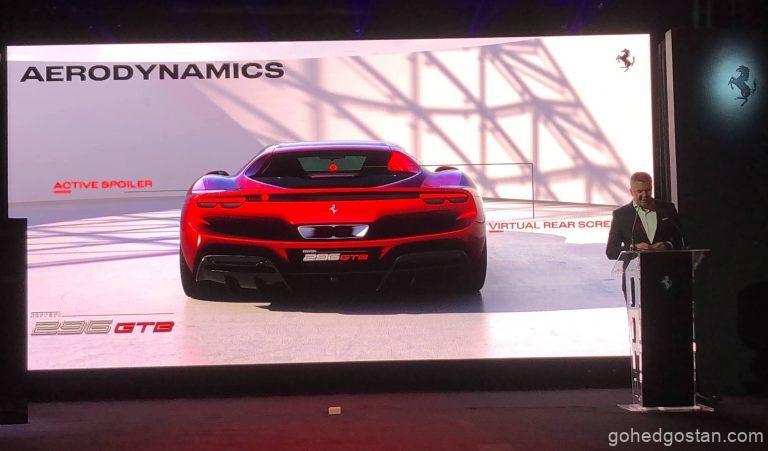
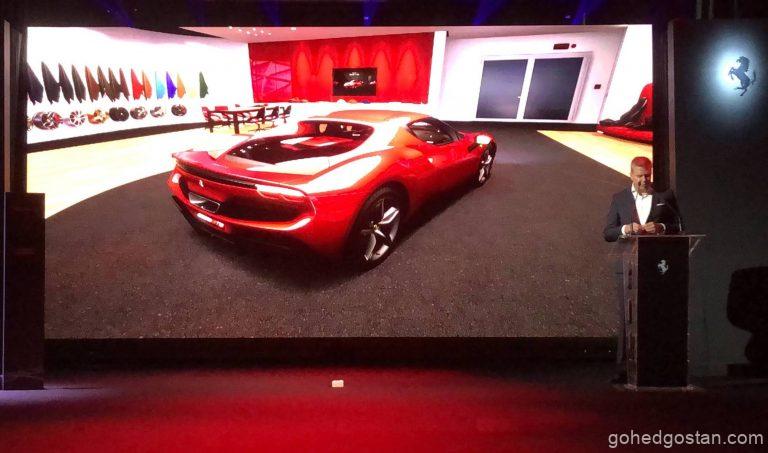
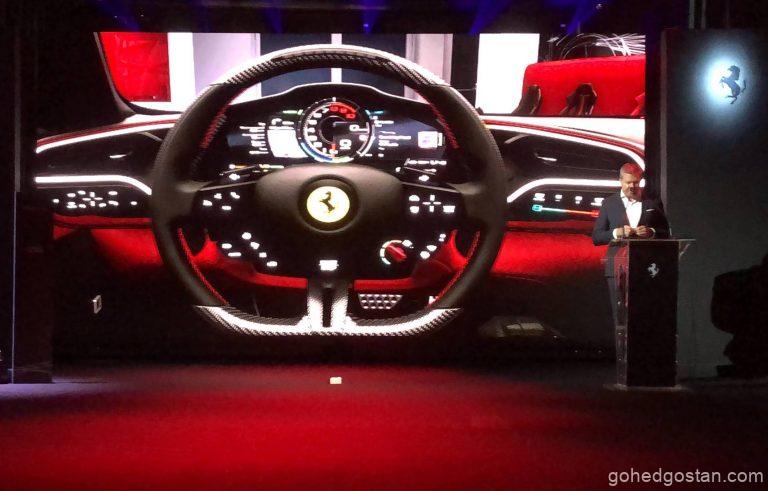
The Ferrari 296 GTB’s inverter is based on two silicon modules connected in parallel, the power deliver mode of which has been optimised to achieve the MGU-K’s torque increase to 315 Nm. This component converts the electric energy with an extremely high level of efficiency (over 94 percent) and can supply the power required to start the V6 even when there is maximum demand for electric power.
No Comment